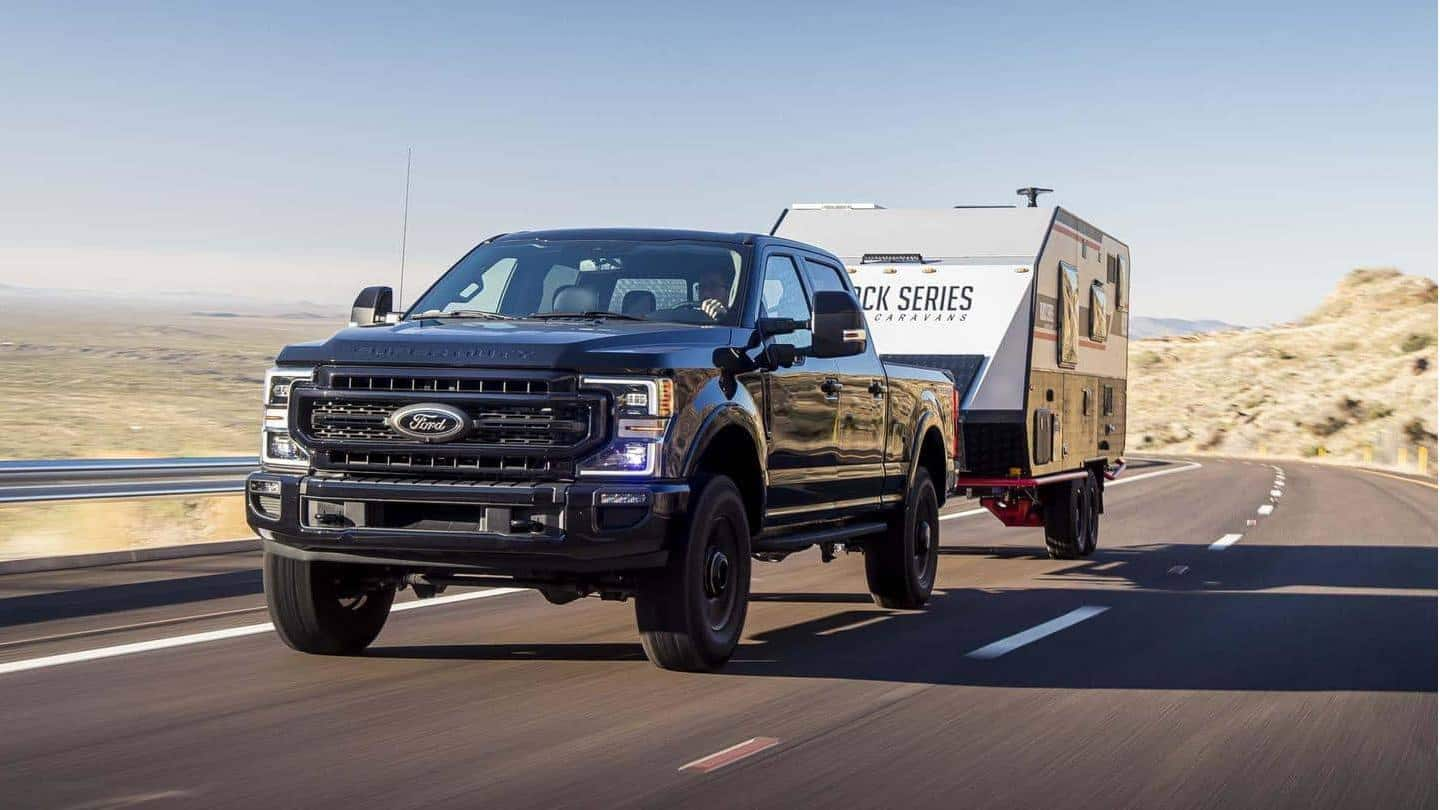
Ford sekarang memproduksi suku cadang F-250 menggunakan limbah printer 3D daur ulang
Apa ceritanya
Produsen mobil Amerika Ford telah bekerja sama dengan HP dan tiga perusahaan lain untuk menggunakan kembali bahan baku pencetakan 3D bekas seperti bubuk dan filamen. Proses baru ini mengubah limbah menjadi bahan yang cocok untuk komponen plastik cetak injeksi untuk kendaraan.
Dalam apa yang disebut Ford sebagai industri pertama, perusahaan ini menggunakan teknik baru untuk memproduksi klip saluran bahan bakar secara massal untuk mobil F-250-nya.
Hemat biaya
Proses pencetakan 3D menambahkan material lapis demi lapis untuk membuat komponen
Ford mengatakan suku cadang yang diproduksi 7% lebih ringan dan juga lebih murah 10%.
Pencetakan 3D adalah proses manufaktur aditif yang menambahkan bahan lapis demi lapis untuk membuat bagian, bukan proses subtraktif konvensional yang menghilangkan bahan. Ini berarti secara inheren membuang lebih sedikit material.
Namun, pemborosan masih terjadi dalam bentuk cetakan yang gagal atau salah, cetakan kalibrasi, dan gulungan untuk filamen.
Detail
Limbah pencetakan 3D Ford tidak langsung dapat digunakan untuk pencetakan injeksi
Ford menggunakan printer 3D HP di Advanced Manufacturing Center untuk membuat purwarupa, perlengkapan yang digunakan oleh pekerja jalur perakitan, dan suku cadang kendaraan komersial bervolume rendah.
Teknologi pencetakan 3D perusahaan itu memerlukan masukan material dalam berbagai bentuk fisik seperti bubuk, cairan, dan filamen.
Namun, limbah cetak dan bahan mentah yang tidak terpakai tidak dapat segera digunakan kembali untuk klip saluran bahan bakar cetakan injeksi.
Tidak ada pemborosan
Ford dan HP bekerja sama dengan Lavergne untuk mengubah limbah menjadi pelet
Cetakan injeksi membutuhkan masukan material dalam bentuk pelet. Di sinilah produsen resin Lavergne masuk.
Perusahaan ini mengubah bubuk dan cetakan yang dibuang dari fasilitas Ford menjadi pelet.
Pelet ini dicetak menjadi klip saluran bahan bakar oleh pemasok Ford, ARaymond, yang juga menangani desain, teknik, dan pembuatan sistem perakitan.
Ford juga terikat dengan SmileDirectClub, perawatan mulut dan platform teknologi medis.
Gimmick pemasaran?
Klip saluran bahan bakar Ford yang menggunakan bahan daur ulang tidak mungkin lebih ringan
Ford mengklaim telah mencapai penghematan bobot 7% pada klip saluran bahan bakar sepuluh gram untuk mobil tiga ton.
Namun, pembuat mobil biasanya menggunakan plastik ABS, nilon, dan polikarbonat untuk pembuatan purwarupa. Material ini lebih padat dari bagian mobil hasil cetak injeksi yang umumnya berbahan PVC, polyurethane, dan polypropylene.
Jadi, ketika bahan baku daur ulang yang lebih padat dicetak dengan injeksi, bagian yang dihasilkan tidak mungkin lebih ringan.
Semua tersenyum
Fasilitas printer 3D HP terbesar di dunia menambah volume untuk Ford
SmileDirectClub juga mengoperasikan fasilitas sistem pencetakan 3D HP terbesar di dunia. 60 lebih printernya menghasilkan lebih dari 40.000 pelurus gigi setiap hari.
Suku cadang cetak 3D bekas ini juga dikumpulkan dan didaur ulang untuk meningkatkan volume produksi pelet untuk Ford.
Meskipun proses tanpa limbah yang baru merupakan pengoptimalan kecil, proses ini dapat memiliki dampak yang cukup besar mengingat skala operasi Ford.